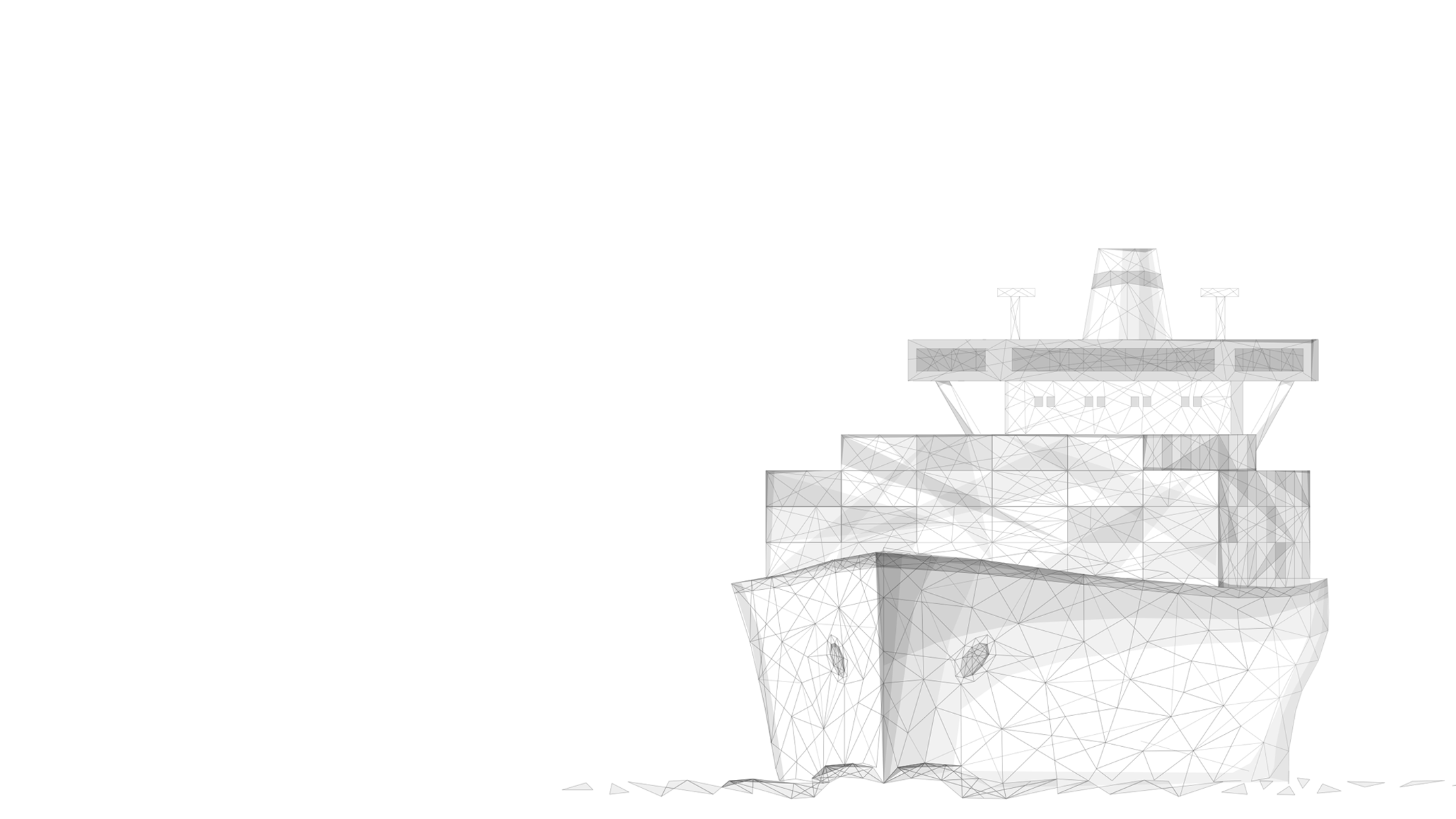
EPC
Engineering Process Clash
Clash Management for PTC Windchill & Creo View
Engineering Process Clash
Detect, understand, resolve collisions – with EPC
Component collisions are among the most common challenges in product development – and are typically expensive when detected too late. With EPC, CADS offers a proven solution to automatically detect, analyze, and clearly visualize collisions throughout the entire product lifecycle. This provides valuable insights into maturity, development status, and potential bottlenecks – enabling informed decisions before problems arise.
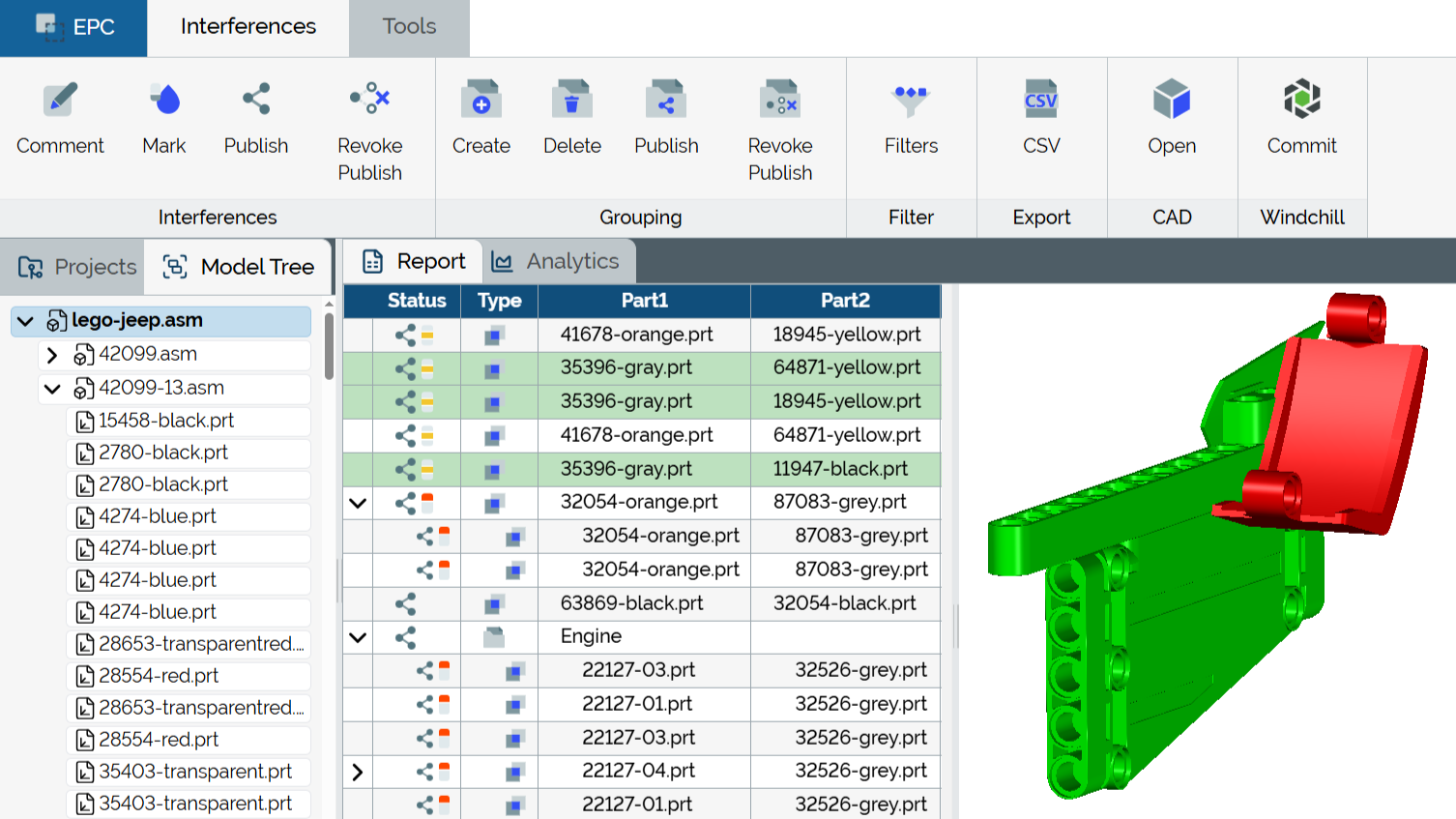
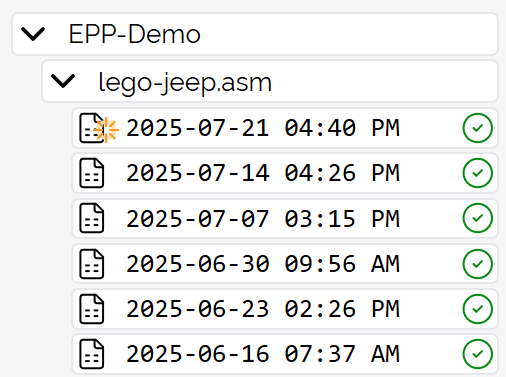
Traceability for the entire component lifecycle
Visualize results – make them tangible
The foundation for detecting component collisions uses PTC's Creo View Interference Engine, whose results are transferred to a collision database. The repeatedly recurring verification process has been designed to be scalable, and collision classifications are automatically carried over to the next verification run. Re-evaluation of already known collisions is no longer necessary.
EPC – Analytics
Analyze results – derive actions
EPC Analytics enables targeted and systematic evaluation of collision data captured with EPC in Creo View and Windchill. The goal is to generate actionable information from the multitude of clash data – for quality assurance, continuous optimization of design and approval processes, as well as effective project management and capacity planning. This transforms every detected collision into measurable value for planning, implementation and strategic engineering decisions.
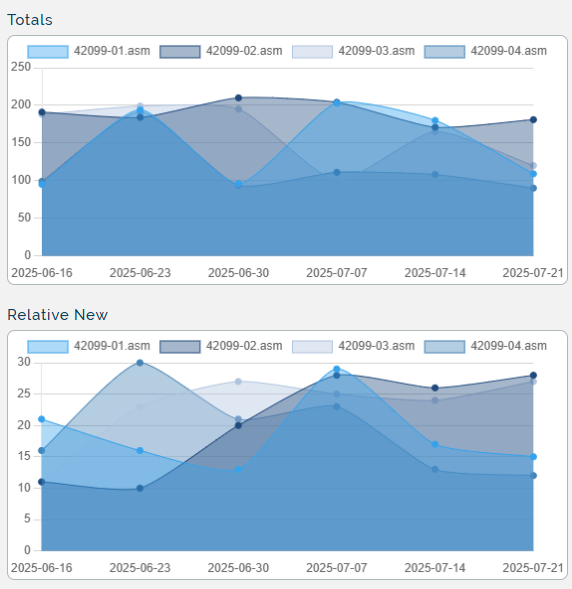
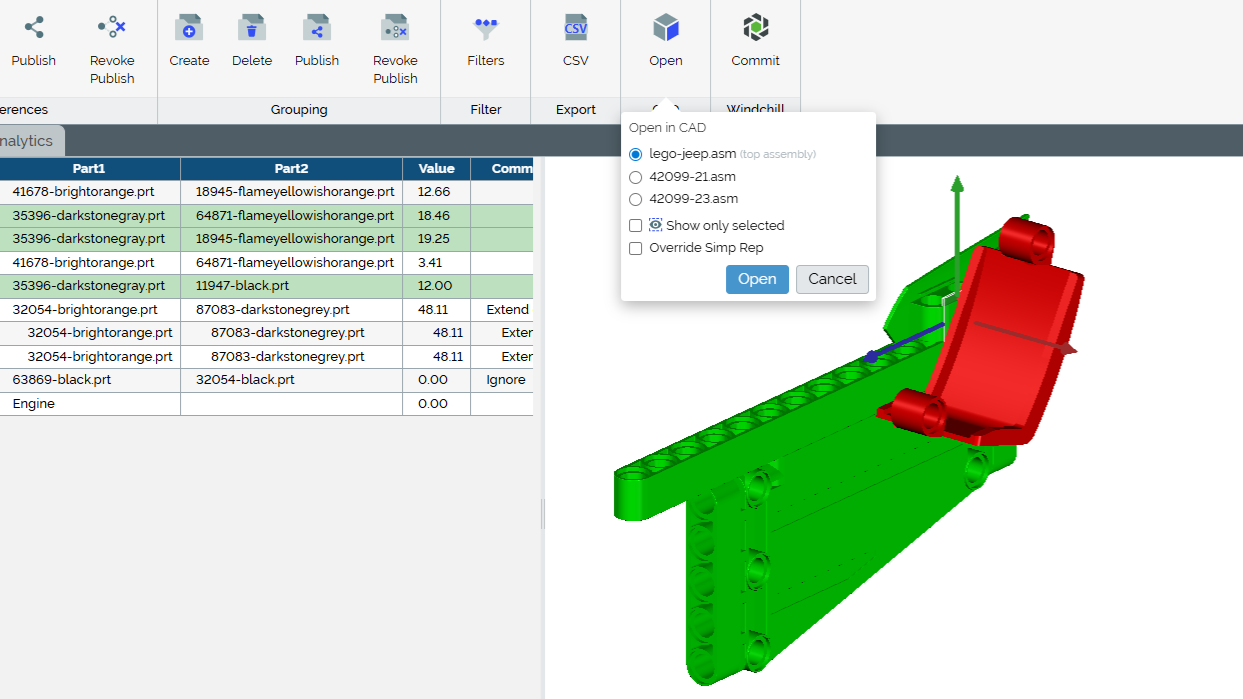
Creo Parametric Integration
Detect collisions early – and edit directly in CAD
EPC is not just a pure 'display system' for collisions, but is fully integrated into the design process. From a detected collision, the affected component can be opened directly in Creo – including exact position and context in the model. This allows designers to respond in a targeted manner, make modifications and efficiently resolve the clash without lengthy searching or detours through other systems.
Seamlessly integrated
EPC transfers only relevant collisions to Windchill – intelligently filtered and grouped. For multiple identical collisions between the same components at different locations, only one representative collision is stored. This significantly reduces the number of objects to manage and makes handling simpler and more efficient.
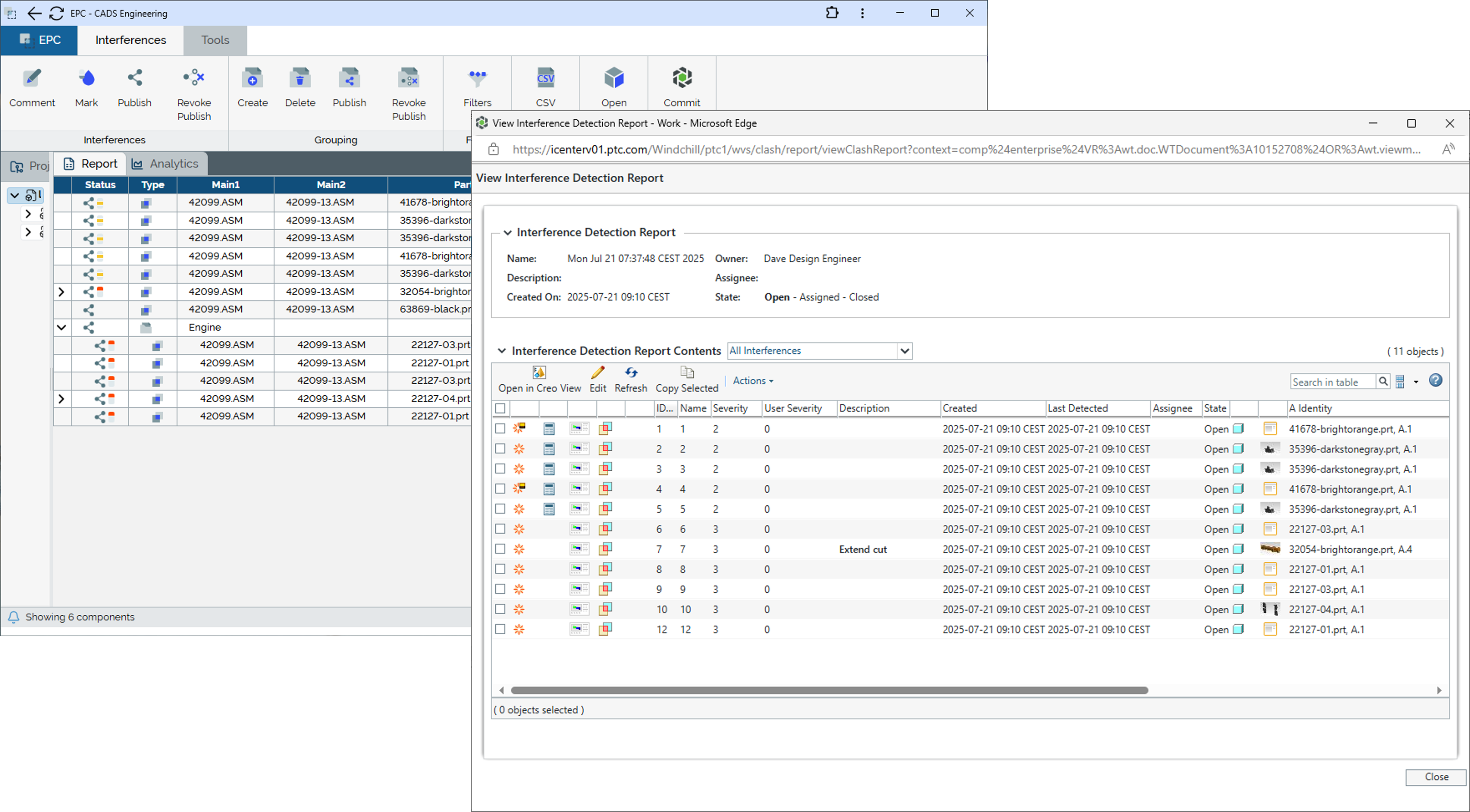
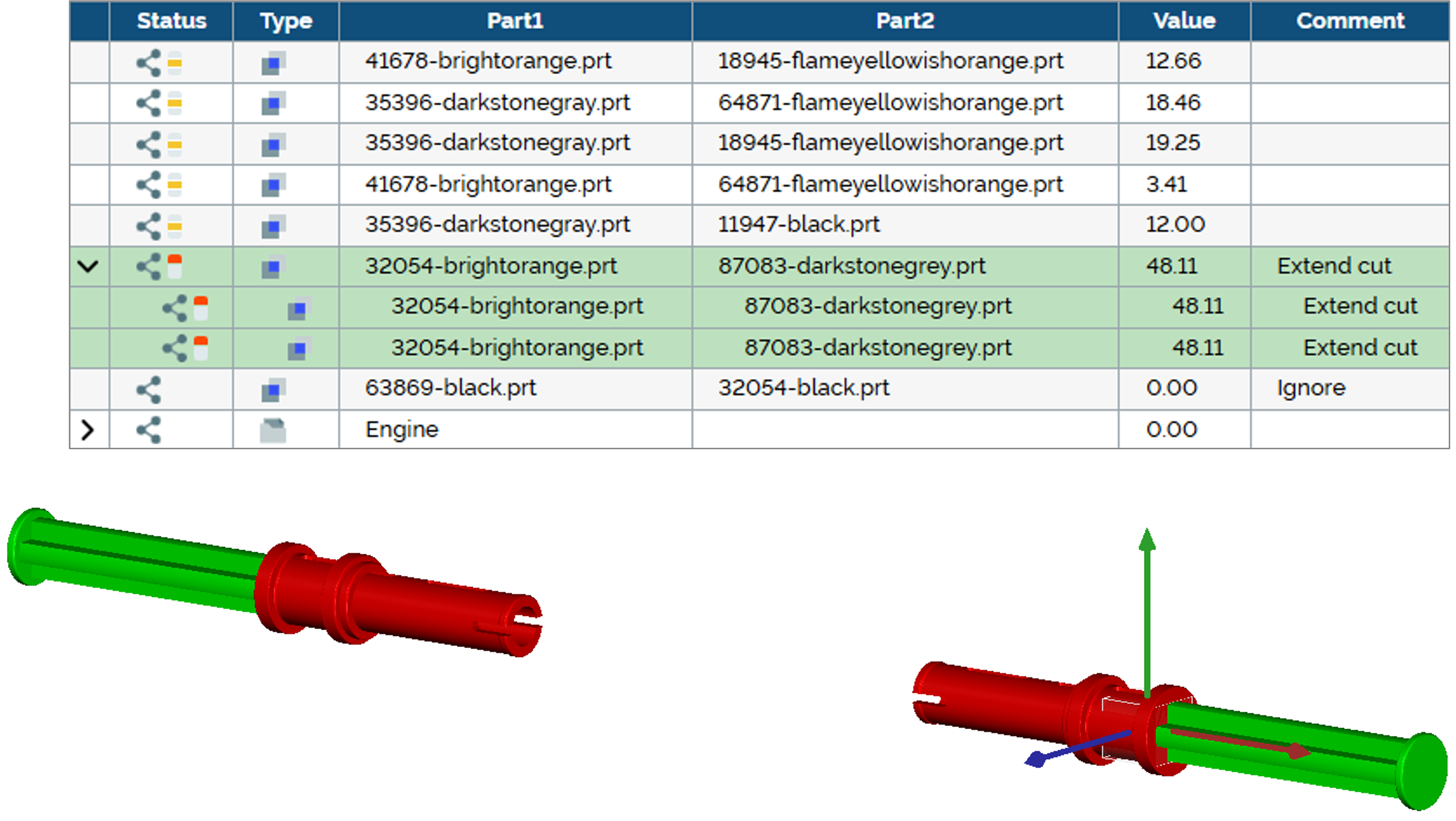
Less is more
Automatic grouping of identical collisions
EPC automatically analyzes recurring collisions or identical component conflicts. Instead of manually checking hundreds of individual conflicts, EPC groups them into logical clusters – efficiently, accurately, and transparently. This helps you maintain overview and significantly accelerate the development process.
Less effort. More insight. EPC in 3 minutes
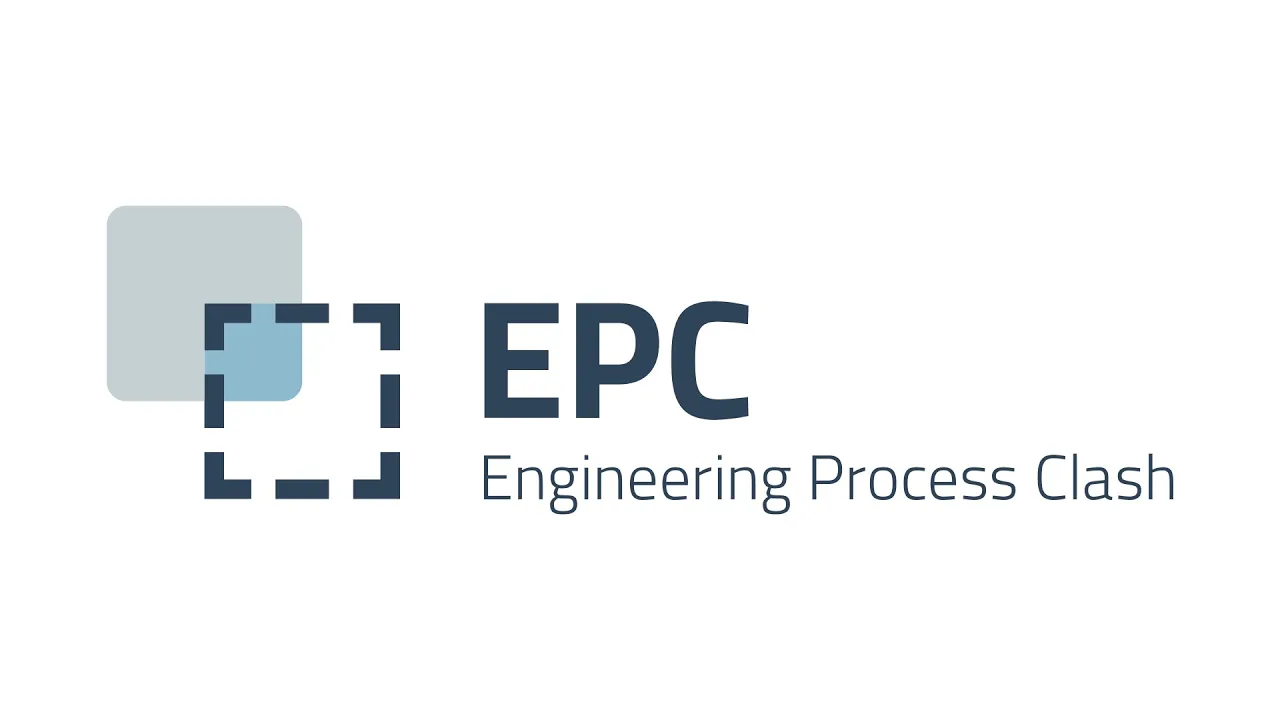
Key Features
Direct CAD integration
Significant reduction in analysis time
Collision tracking throughout the entire lifecycle
Fully integrated with PTC Windchill
Systematic monitoring of collision analyses
Benefits
Collision management can also be performed by non-CAD users
Comprehensive clash detection across all project phases
Automated grouping and classification of similar collisions
Contact us
Discover how we can help you! Reach out to us for more information or support.